Production of wood veneer
From the tree to wood veneer
Before a tree trunk becomes a veneer, many steps are required. The most important steps are shown below.
- Buying
- Storing and bark stripping
- Cutting to length
- Cooking / Steaming
- Slicing / Peeling
- Drying, cutting, grading
Buying
Although state-of-the-art technology is used today in veneer production, manufacturing requires great experience and craftsmanship. Only professionals can already recognize the quality of a strain in the forest and select it for veneer production. Each type of wood is individually processed and assembled.
Here, experts decide trunk by trunk, with which technique from the round wood, the veneer is produced. In order to meet the quality requirements of the veneer processing industry and the consumer, it requires a great deal of experience in the purchase of logs so that optimum processing is guaranteed.
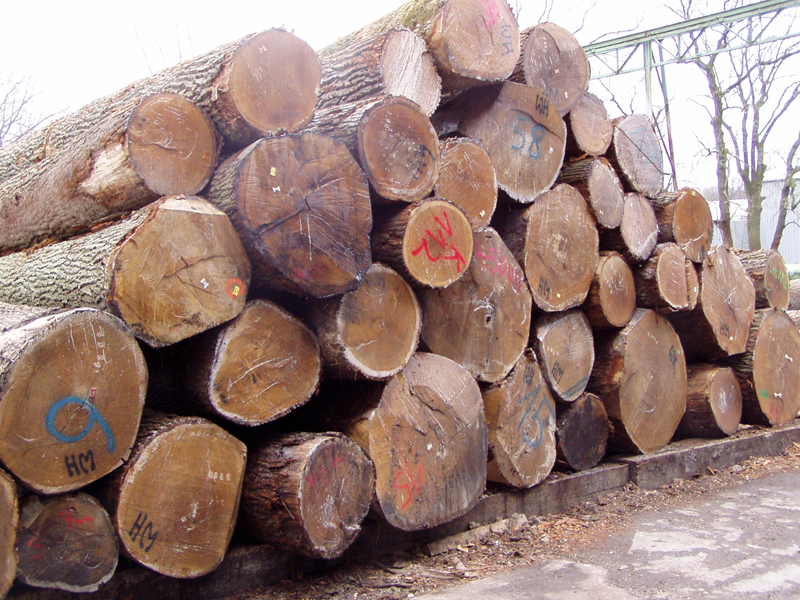
Storing and bark stripping
In order to store logs properly, they must be continuously sprinkled with water. The moisture prevents changes in colour and cracking caused by drying. The bark is removed (stripped) from the raw wood to prepare it for the slicing and peeling machines. At the same time, any foreign materials such as pressed in stones, hammered in nails, sand and soil are removed.
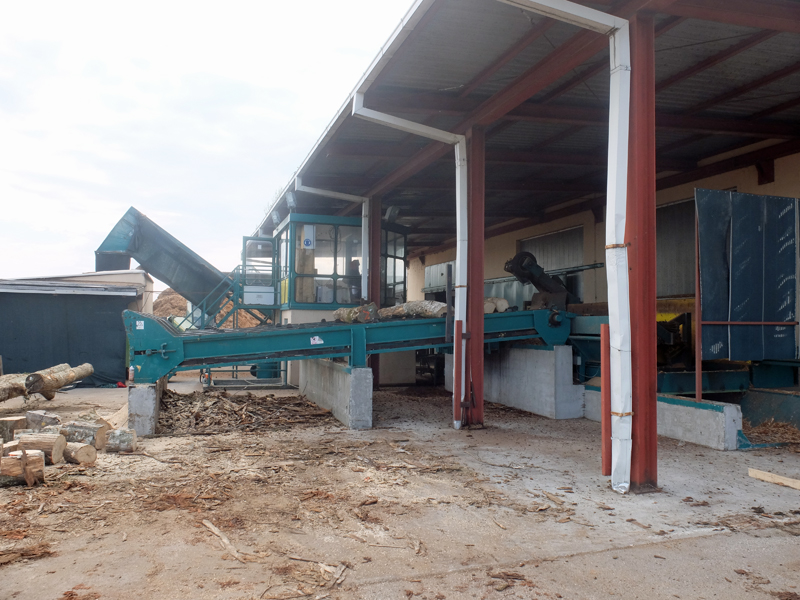
Cutting to length
In order to achieve optimum use and quality grading (qualitative classification), the logs are classified in sections by growth features, shape and length specifications. They are marked for the subsequent sawing open according to their shape and heartwood crack (so-called heart shake - a radial crack originating in the pith)
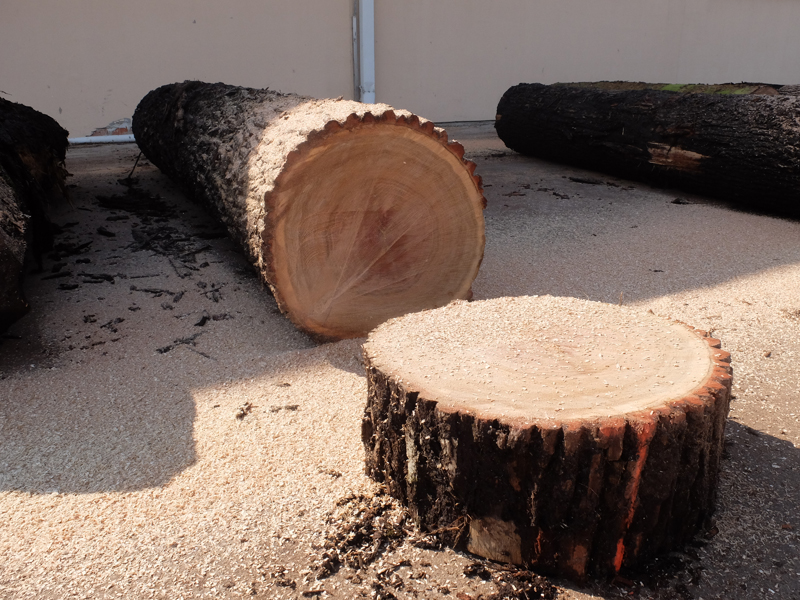
Cooking / Steaming
Cooking or steaming in hot water achieves two effects:
- The wood acquires the necessary pliability, in order to ensure a smooth cut and therefore perfect preparation quality.
- The duration of the cooking or steaming process affects the colour of the veneer.
Depending on the wood species and colour required, steaming periods of one day to two weeks is necessary.
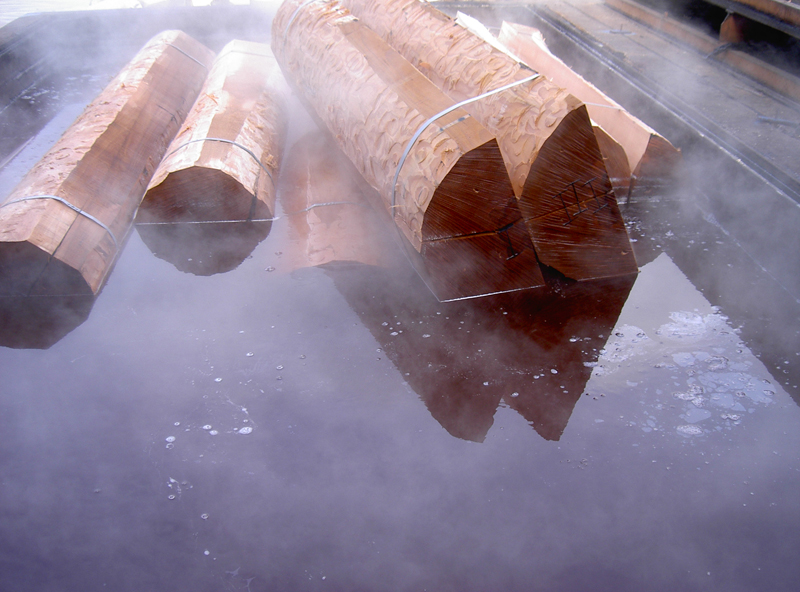
Slicing / Peeling
In the next step the wood is cut into thin layers – or as the experts say, "sliced" or "peeled". A differentiation is made between two types of machines for veneer preparation: Slicing machines and peeling machines, as well as different types of preparation.
Different results are obtained, depending on which machine and which type of preparation is used. For the quality of the preparation, it is decisively important for the blade to be set precisely with an accuracy of 0.1 mm. Only then can faultless quality be guaranteed.
More information on slicing and peeling is given here:
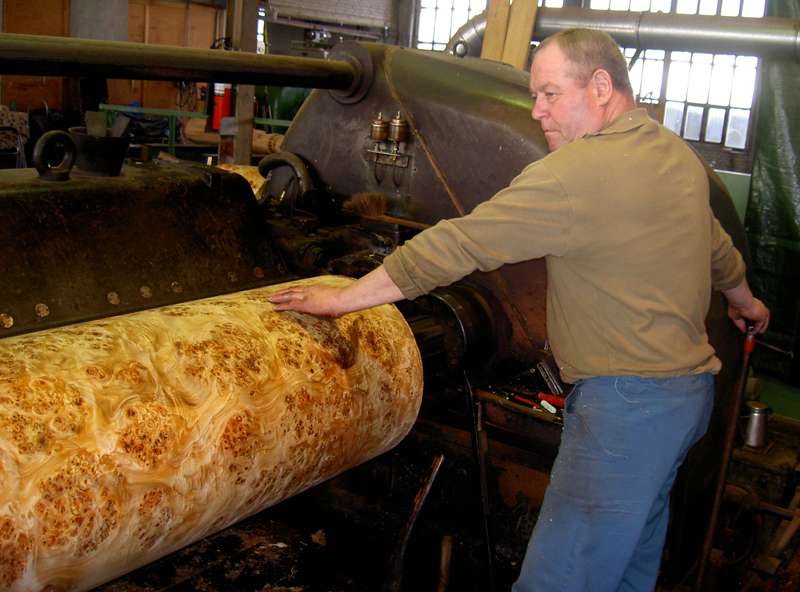
Drying, cutting, grading
The still wet veneer sheets are dried in dryers, which also have an ironing effect. Different throughput times and temperatures are also selected for drying, depending on the wood species. Veneers that are too dry are crumbly and cannot be used any further, veneers that are too moist can become mouldy and are then also no longer usable.
When the veneers are dry they are properly bundled and cut. The edges are straightened and if necessary growth irregularities are cut out. The producer pre-grades special qualities according to the diverse intended uses. This is done according to the customer's specifications regarding dimensions, figure and price.
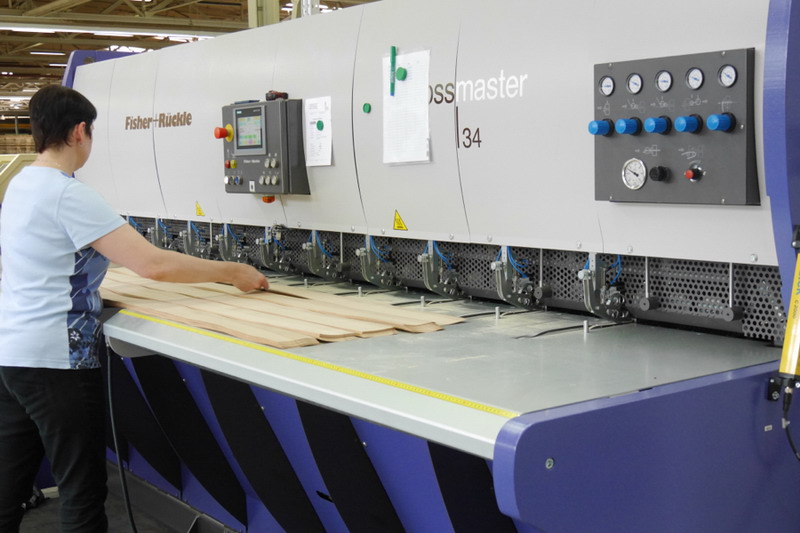